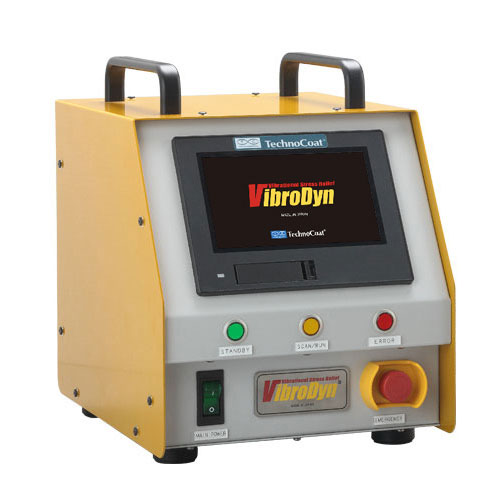
Vibrational Stress Relief
VibroDyn
VibroDyn is an equipment to alleviate or remove internal stress in metals using vibrational energy
The resonance waveform can be visualized by a simple operation, and the natural resonance point of the workpiece can be detected and easily processed with vibration effective for stress reduction.
The resonance waveform can be visualized by a simple operation, and the natural resonance point of the workpiece can be detected and easily processed with vibration effective for stress reduction.
VibroDyn Features
Significant reduction in processing time and outsourcing cost
Repeated heating and cooling seen in the processes, machining, welding, casting, etc., generates internal stress and causes distortion and cracks.
In general, the stress is relieved by heat treatment in annealing furnaces, but VibroDyn does it comparably good without using heat or space-energy-consuming facilities
In addition, VibroDyn process is a shorter leading-time and 1/10 costs of equipment and processing comparing to heat treatment, and energy consumption is less than 1/100 earth environment-friendly Eco Machine.
VibroDyn is a newer Vibrational Metal Internal Stress Relief and Metal Stabilization equipment.
In addition, VibroDyn process is a shorter leading-time and 1/10 costs of equipment and processing comparing to heat treatment, and energy consumption is less than 1/100 earth environment-friendly Eco Machine.
VibroDyn is a newer Vibrational Metal Internal Stress Relief and Metal Stabilization equipment.
Activates atomic movements and corrects defects in atomic structure
Residual stress is synonymous with lattice defects on metal's atom arrangement.
To relieve the stress, heat treatment is often used in general but physical vibration is also able to correct the lattice imperfection and relieve internal stress.
Three theories are reported below.
1. Effective Number of Vibration (Vibration at a resonance point is optimal for stress relief)
2. Resonance Point Movement (Resonance point moves down along the degree of stress relief)
3. Resonance Point Stability (Resonance Point will be stable since stress relieved)
To relieve the stress, heat treatment is often used in general but physical vibration is also able to correct the lattice imperfection and relieve internal stress.
Three theories are reported below.
1. Effective Number of Vibration (Vibration at a resonance point is optimal for stress relief)
2. Resonance Point Movement (Resonance point moves down along the degree of stress relief)
3. Resonance Point Stability (Resonance Point will be stable since stress relieved)
Processing Methods
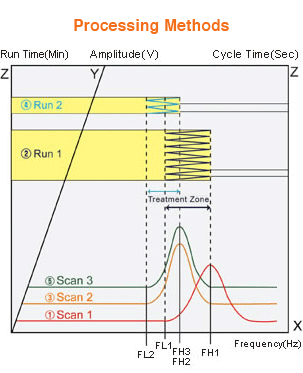
❶ Scan1 | Resonance Range Measurement To measure frequency of a point of increasing vibration amplitude (FL1) and a resonance point (FH1). |
---|---|
❷ Run1 | Vibration (Stress Relief) To vibrate for 15 - 30 min. during frequency of FL1 and FH1. |
❸ Scan2 | Resonance Range Remeasurement To measure FL2 and FH2. |
❹ Run2 | Re-Vibration (Stability Confirmation) Final measurement of Resonance Point (Finish Processing) |
❺ Scan3 | Final measurement of Resonance Point (Finish Processing) To be closed the processing when FH3 and FH2 are coincidence. To repeat the process "4" to "5" till coincide with FHn-1. |
In VibroDyn, the resonance zone (Resonance Zone) between the frequency (FL: Frequency Low) at the point where the amplitude starts to rise and the frequency (FH: Frequency High) at the resonance point when the frequency of the work is gradually increased.
Vibration is processed with the frequency of reciprocating
Vibration is processed with the frequency of reciprocating
Stress Occurrences Causes & Issues
Stress Occurrences Causes | Machining |
---|---|
Welding | |
Casting | |
Forging | |
Heat Treatment | |
Heat Treatment |
Stress Issues | Distortion |
---|---|
Cracking | |
Stress Corrosion | |
Fatigue Fracture | |
Brittle Fracture | |
Heat Treatment |
Actual measurement result
-
Annealed material
About 90Mpa compression -
Quenched material
About 230Mpa compression -
Tempered material
About 250Mpa compression
●=Before processing
●=After processing
Sample | Material | Heat treatment | Grinding | Condition | Vibration frequency (Hz) | Change in stress after vibration |
---|---|---|---|---|---|---|
1 | SKD61 | Untreated | Grinding | Machining after purchase | 14 to 16 | 200Mpa compression |
2 | SKD61 | Annealed, Furnace cooling | Prefinished | Annealing | 90Mpa compression | |
3 | SKD61 | Quenched | Grinding | Machining after quenching | 230Mpa compression | |
4 | SKD61 | Quenched, Tempered | Grinding | Before nitriding | 250Mpa compression | |
5 | SKD61 | Mold | Finish | Over 5,000 shots | 152Mpa compression |
Material that can be processed
Low / medium / high carbon steel, alloy steel, tool steel, stainless steel, manganese steel, Inconel, aluminum alloy, titanium alloy, cast iron, cast steel, aluminum die casting / casting products, forged products and their welded structures, etc. |
Heat treatment and VibroDyn comparison
Process / Items | VibroDyn | Heat treatment |
---|---|---|
Transportation | Equipment is movable to the site of objects without any time and cost of transportation. | Time and cost necessary for transportation of objects to a vendor. |
Size | Able to process large or heavy objects, dealing part by part of a large object in several times. | The size of annealing furnace is limited, and a large object can not be accommodated. |
Time | Generally, this process will be done within 1 hour. | Processing time taking longer and lead-time might be an issue. |
Problems | These problems are not occurred by this process. | Hardness change, oxidization, scale formation, etc. |
Equipment Cost | The cost is 1/10 or less comparing to Heat Treatment. | Require expensive capital investment. |
Skill | Easy operation and no advanced technology and skills required. | Advance technology and skills are required. |